Conference Programme
Day one: Tuesday, 8th July 2025
- Registration | 0830-0900
Please sign in and collect your badge
There will be refreshments available and a chance to see posters and network before the start of the first session
- Session 1A | 0900-1110 | Chaired by: , &
0900 Welcome
0915 Keynote talk
Jeff Bunn | Oak Ridge National Laboratory, USA
Harnessing Neutron Scattering for Next-Generation Materials Engineering
The U.S. national laboratory system has been a cornerstone of scientific innovation, providing large-scale research infrastructure beyond the capabilities of academia and industry. Among these institutions, Oak Ridge National Laboratory (ORNL) has led advancements in neutron science for over five decades, housing two of the world’s most advanced neutron research facilities: the High Flux Isotope Reactor (HFIR) and the Spallation Neutron Source (SNS). This presentation will explore how neutron scattering techniques—including neutron diffraction, small-angle neutron scattering (SANS), and neutron imaging—enable unprecedented characterization of engineering materials. Unlike conventional methods such as X-ray diffraction, neutron-based techniques allow for deep, non-destructive analysis of internal stress distributions, phase transformations, and nanoscale structures, making them invaluable for aerospace, nuclear energy, automotive, and heavy industry applications. Key examples will highlight how neutron scattering enhances our understanding of structural materials, including weld integrity, additively manufactured components, and fatigue-sensitive alloys. Additionally, attendees will learn how to access ORNL’s world-class neutron facilities through proposal-driven user programs, opening opportunities for groundbreaking research in materials science. By integrating neutron-based methods, researchers can drive innovation in structural integrity, failure prevention, and next-generation materials development.
0945 Researcher Presentations
Olivia Broadbent-Clark | СŷÊÓÆµ of Manchester
Improving the Tolerance of Aluminium Alloys to Impurity Elements
The properties of aluminium alloys are greatly influenced by their composition and subsequent heat treatment. In this study the phases present during solidification and changes that occur during homogenisation are investigated in AA3104 and two recycled variants. Microstructural characterisation was performed using optical and scanning electron microscopy along with differential scanning calorimetry, with results compared to JMatPro simulations. The as-cast microstructure contained Al6(Mn,Fe), α-Al(Mn,Fe)Si, and Mg2Si phases with additions of T-AlCuMg in some alloys. During homogenisation, Mg2Si dissolved and the Al6(Mn,Fe) phase transformed into the α-Al(Mn,Fe)Si phase. Increased magnesium content decreased the rate of Mg2Si dissolution and decreased the rate of Al6(Mn,Fe) to α-Al(Mn,Fe)Si transformation.
Merve Yesim Yalcin | СŷÊÓÆµ College Dublin
Influences of Oxide Dispersoids on Microstructural Evolution and Cytocompatibility of ODS-Modified Ti-6Al-4V Alloys
Co-authors: Merve Nur Dogu (Dublin City СŷÊÓÆµ), Dermot Brabazon (Dublin City СŷÊÓÆµ), Mert Celikin (СŷÊÓÆµ College Dublin)
Ti-6Al-4V is a commonly used alloy in biomedical implants. However, columnar prior beta grains form at elevated temperatures during production and transform into acicular alpha prime laths during rapid solidification. These coarse microstructure constituents cause texture formation and stress localization, therefore degrading the mechanical stability of implants. In this study, to enhance the mechanical stability of the alloy, the formation of oxide dispersoids in the matrix phase is promoted to refine and stabilize the microstructure. ODS-modified Ti64 alloys are designed and produced through the powder metallurgy route; their microstructure evolution and cytocompatibility responses are investigated.
Sydney Coates | СŷÊÓÆµ of Manchester
Understanding Cold Work Needed for Recrystallization of 316 LPBF Material and its Effect on the Material's Performance in PWR Primary Water
Co-authors: Fabio Scenini (СŷÊÓÆµ of Manchester), Ed Pickering (СŷÊÓÆµ of Manchester), Timothy Watkins (Rolls Royce), Karen Perkins (Rolls Royce)
As additive manufacturing becomes a more utilized manufacturing process, switching to laser powder bed fusion to create 316 stainless steel structural components for nuclear reactors is considered. However, current post-build HIPPing treatments aren’t able to erase the as-built laser scanning tracks, resulting in an inhomogeneous microstructure that increases the material’s susceptibility to stress corrosion cracking initiation. Because of this, induced cold work with a follow-up solution annealing heat treatment are used to produce an evolution of recrystallized microstructures. These microstructures have currently been analysed and will have SCC initiation tests done to compare their performance to the as-received material.
Grace Fidler | СŷÊÓÆµ of Manchester
Retained Austenite Decomposition in Low Alloy Steels
Low-alloy steels are used in a variety of applications as structural materials. They are often heat-treated to form microstructures comprising hard. Typical heat treatment usually comprise austenitisation, quenching and tempering steps. Following quenching, it is often found that small amounts of austenite remain untransformed at room temperature, called retained austenite. While the amount of this is small, it may influence the final microstructure and properties of the final component after tempering. The work uses XRD with Rietveld refinement and EBSD to measure the amount of retained austenite in the sample. Additionally, quench dilatometry is used observe austenite decomposition in situ.
1105 Poster Flash Presentations
1 | Gavin Chapman | Dublin City СŷÊÓÆµ
Multi-Sensor In-Situ Monitoring and Porosity Prediction in Powder Bed Fusion of Nitinol (NiTi)
Co-authors: Mert Celikin (СŷÊÓÆµ College Dublin), Claudia Mazo (Dublin City СŷÊÓÆµ), Dermot Brabazon (Dublin City СŷÊÓÆµ)
Powder Bed Fusion-Laser Beam (PBF-LB) is widely used in biomedical manufacturing for its precision in producing complex geometries, though porosity remains a key challenge. This study integrates acoustic emission and infrared thermography sensors into a PBF-LB system to monitor the fabrication of Nitinol (NiTi) samples under varying process parameters. A 4×4 full factorial design was used, and porosity was assessed via the Archimedes method. Machine learning algorithms were developed to predict density outcomes, forming a digital twin model for porosity prediction and future control. This approach enables the framework for adaptive processing and improved quality control for NiTi components.
2 | Ankar Majumdar | Dublin City СŷÊÓÆµ
Mechanical Characterisation of PBF-LB and Heat-Treated Nickel-Rich NiTi Lattice Structures
Co-authors: Joseph Michael Doyle, Lehar Asip Khan, Ankur Majumdar, Dermot Brabazon
Nickel-rich NiTi alloys produced through metal additive manufacturing (AM) allow for the creation of complex shapes with minimal post-processing. This study focused on manufacturing porous NiTi lattice structures using laser powder bed fusion (PBF-LB), followed by detailed mechanical, thermal, and physical characterization. A 10% variation in strut diameters of the printed samples was observed compared to CAD models. The energy-dispersive X-ray spectroscopy (EDX) revealed a nickel loss of up to 1 at.% with the final part still with a predominantly austenitic parent phase. Full-field stress- displacement analysis showed the as-printed lattices achieved a peak energy absorption efficiency of 21.03%. Experimental stress strain results aligned well with preduiction from Auricchio’s model for phase transformation stress-strain. Extending this work, the heat-treated NiTi lattice structures were examined to understand how post-processing affects microstructural evolution, phase transformation, mechanical properties, and overall performance, thereby providing insights into optimizing these additively manufactured NiTi lattices for advanced applications.
3 | Achu Mavelil Titus | Dublin City СŷÊÓÆµ | 3D printed nickel based alloys as anode material for sodium ion batteries
Co-authors: Anesu Nyabadza (Dublin City СŷÊÓÆµ), Sithara P. Sreenilayam (Dublin City СŷÊÓÆµ), Dermot Brabazon (Dublin City СŷÊÓÆµ)
Sodium-ion batteries have emerged as a promising alternative to conventional lithium-ion batteries due to their comparable electrochemical performance. However, the technical challenges related to stabilising cathodes, anodes, and electrolytes hinder the development of sodium-ion batteries like lithium-ion batteries. The anode material should be highly conductive and maintain a voltage close to pure sodium. Sodium-ion batteries typically avoid using pure sodium as the anode because it reacts with organic electrolytes, forming an unstable and ineffective passivation layer. Various forms of carbon, transition metal oxides, alloys, metal oxides, sulphides, and organic composites have been used as anode material for developing sodium-ion batteries. This work introduces 3D printed nickel based alloy as an anode for developing sodium ion batteries. Its high electrical conductivity, chemical stability, and surface properties have the potential to lead to enhance battery performance. These developments offer a promising strategy for creating an anode material to advance high-performance sodium-ion batteries.
- Refreshments and Posters | 1110-1140
- Session 1B | 1140-1300 | Chaired by: , &
1140 Researcher Presentations
Deeksha Hota | СŷÊÓÆµ College Dublin
Effect of Varying Overhang Length in L-PBF Printed Ti-6Al-4V Parts
Co-authors: Di Nguyen (СŷÊÓÆµ College Dublin), Denis Dowling (СŷÊÓÆµ College Dublin)
Overhang geometries present a considerable challenge for laser powder bed fusion manufacturing due to reduced heat dissipation ability of the metal powder under the overhang. This leads to overheating related defects such as porosity, spatter, surface roughness, and distortion. This study investigates the influence of overhang lengths, varied in the range of 2–10 mm on the quality of Ti-6Al-4V components. Metallurgical analysis is conducted to evaluate microstructural variation and defect formation. Optical and thermal emissions obtained from in-situ process monitoring are analysed to assess the sensitivity of the PM system in detecting defects.
Eamonn Lawlor | СŷÊÓÆµ of Manchester
Ti-6Al-4V cold dwell fatigue loading - effect of stress concentrations and fatigue crack growth rates
Co-authors: Alec Davis (СŷÊÓÆµ of Manchester), Joao Quinta Da Fonseca (СŷÊÓÆµ of Manchester), Benjamin Dod (Airbus), Nicholas Byers (Airbus)
Cold dwell fatigue, where the maximum tensile stress is held constant for a period during each load cycling, can result in a significant fatigue lifetime debit in titanium alloys. It remains unclear how dwell fatigue effects fatigue crack growth (FCG) rates in this material. This study investigates the effects of dwell loading around stress concentrators and on fatigue crack growth rates in Ti-6Al-4V. Samples were subjected to three-point bend tests to study FCG rates under cyclic and dwell fatigue. High resolution digital image correlation was conducted on notched microtensile samples to compare slip activity under instantaneous and dwell loading.
Dillon Frith | СŷÊÓÆµ of Sheffield
The Replication of Defects in Titanium Aerospace Components Using Field-Assisted Sintering Technology (FAST) and the Analysis Method Force Response Mapping (FRM)
This presentation explores the application of Field-Assisted Sintering Technology (FAST) to replicate defects in titanium alloys, enabling a controlled approach to studying defect formation and behaviour. Analysis was conducted by means of Force Response Mapping (FRM) and Ultrasonic Testing (UT) to assess the fidelity of defect replication. This work provides insights into FAST and how the method can be used to create desired features within a material through the use of metallic powder.
Riccardo Sorrill | СŷÊÓÆµ College Dublin
Towards Real-Time Anomaly Detection of Recoater Malfunction
This study proposes a potential path toward real-time anomaly detection of recoater malfunctions during the powder-distribution in stainless-steel Laser-Powder Bed Fusion. The approach isolates melt-pool emissions for each individual track. It then employs a combination of feature selection and an autoencoder trained to learn a low-dimensional representation of the data, minimizing reconstruction error to establish baseline behavior. The model is semi-supervised and requires training solely on defect-free samples. Anomalies are flagged via a binary classification based on deviations of the reconstruction error from the established baseline. Current work demonstrates a 70% accuracy in detecting recoater anomalies within a window of 20 consecutive laser tracks.
1300 Poster Flash Presentations
4 | Precious Onyeji | South East Technological СŷÊÓÆµ
Optimizing Laser Powder Bed Fusion alloy feedstocks via Nanoparticle reinforcement
Co-authors: Abhijit Cholkar (South East Technological СŷÊÓÆµ), Ronan McCann (South East Technological СŷÊÓÆµ and Dublin City СŷÊÓÆµ), David Culliton (South East Technological СŷÊÓÆµ), Ramesh Ragavendra (South East Technological СŷÊÓÆµ)
Laser Powder Bed Fusion (LPBF) is gaining traction across a variety of sectors due to its ability to fabricate intricate geometries, while minimizing material waste. However, achieving optimal material properties such as low porosity remains a key challenge with this technique. In this study, Ti-6Al-4V is reinforced with Graphene Oxide (GO) to fabricate LPBF parts. The resulting build is systematically characterised, and its mechanical and microstructural properties compared with parts produced from using Ti-6Al-4V. The aim of this is to enhance the material properties of LPBF-fabricated components, offer improved performance and expand its applicability in advanced manufacturing sectors.
5 | Christopher O'Hara | Atlantic Technological СŷÊÓÆµ Slingo
The Application of Metal Additive Manufacturing Technologies to Post-Process Biomedical Metallic Surfaces
Co-authors: Marion McAfee (Atlantic Technology СŷÊÓÆµ and СŷÊÓÆµ College Dublin), Ramesh Raghavendra (СŷÊÓÆµ College Dublin, South East Technological СŷÊÓÆµ) , Dermot Babazon (Dublin City СŷÊÓÆµ), Merve Nur Dogu (Dublin City СŷÊÓÆµ), Meris Ikiz (Dublin City СŷÊÓÆµ), Usman Aziz (Atlantic Technology СŷÊÓÆµ and СŷÊÓÆµ College Dublin), David Tormey (Atlantic Technology СŷÊÓÆµ and СŷÊÓÆµ College Dublin)
This work gives an overview of the progress on post-processing of biomedical metal surfaces, leveraging metal additive manufacturing (AM) to produce, process and control biomedical implant surface properties. This presentation will provide an overview of the developed AM-assisted post-processing workflow, which has been tested on AM 316L stainless steel using AM copper electrodes and also adapted for use on AM NiTi shape memory alloy. The primary focus of the work is to reduce the material, energy consumption and processing steps for manufacturing implants and improve the surface characteristics of biomedical components while controlling their mechanical and biomedical performance.
6 | Blánaid Fogarty | South East Technological СŷÊÓÆµ
Inkjet Printing of Silver Nanoparticle Inks for Conductive Tracks in Printable Electronic Applications
Co-authors: Abhijit Cholkar (South East Technological СŷÊÓÆµ), Dermot Brabazon (Dublin City СŷÊÓÆµ), Ronan McCann (Dublin City СŷÊÓÆµ and South East Technological СŷÊÓÆµ), Ramesh Raghavendra (South East Technological СŷÊÓÆµ)
The demand for compact, flexible electronics has focused research on nanomaterials to reduce size and achieve novel flexibility while offering enhanced electrical characteristics. This work will focus on the optimisation of piezoelectric-pneumatic inkjet printing of silver nanoparticle inks onto flexible, polymer substrates for high resolution conductive tracks and coatings. Post-print sintering will also be investigated and optimised. Characterisation techniques will include adhesion and bend tests for mechanical durability, 4-point probe conductivity and microscopy to determine optimum conditions to achieve repeatability and uniformity. Ultimately, this research aims to improve the feasibility of inkjet printing as an electronic device manufacturing process.
- Lunch, Posters and Career Talks | 1300-1400
There will be the opportunity at this time to view the Poster Exhibition
From 1325 there will be a series of career talks from alumni and industry representatives
- | HMG Paint Ltd | 2012 cohort
- | Manufacturing Simulation Ltd | 2012 cohort
- Westinghouse AB | 2015 cohort
- Marks & Clarke | 2016 cohort
- | СŷÊÓÆµ of Manchester | Staff
- Session 2A | 1400-1530 | Chaired by , &
1400 Keynote talk
Prof. Moataz Attallah | СŷÊÓÆµ of Birmingham
I Find Your Lack of Toughness Disturbing: Control of Microstructures for Performance
The mechanical performance of additively manufactured alloys is intrinsically linked to their microstructure. This talk explores the role of microstructural control during additive manufacturing of high-performance materials. AM offers unprecedented flexibility in controlling the microstructure at different length scales, which impacts the overall material performance. Additionally, by employing in-process microstructural control and post-processing thermal treatments using hot isostatic pressing (HIP) and tailored heat treatments, this combination can enhance the mechanical performance for various applications. We present strategies to optimise the material’s microstructure for improved resistance to fatigue. This research paves the way for the development of more durable and reliable AM’ed materials, essential for next-generation high-performance engineering applications.
1430 Researcher Presentations
Jack Krohn | СŷÊÓÆµ of Sheffield
An investigation into the effect of FAST cooling rates on the lamellar microstructure in Titanium Aluminide GE4822
Field Assisted Sintering Technology (FAST) is a promising solid-state processing method for sintering challenging materials like titanium aluminides. FAST enables precise microstructural control, yet inconsistencies in phase diagrams and microstructure development highlight the need for a clear preprocessing strategy. This study examines the impact of cooling rates after dwell at various temperatures on lamellae formation in the titanium aluminide alloy GE4822. Results show that a dwell temperature of 1350°C is necessary for significant lamellar volume, with the microstructure being highly sensitive to cooling rate. At temperatures above 1375°C, a high lamellar fraction is consistently achieved, independent of cooling rate.
Sunil Yadav | СŷÊÓÆµ of Galway
A micromechanical framework for fatigue life prediction of NiTi using EBSD based CPFE modelling
Co-authors: Dermot Brabazon (Dublin City СŷÊÓÆµ), Sean Leen (СŷÊÓÆµ of Galway)
NiTi alloys are ideal candidates for aerospace actuators due to the shape memory effect activated by change of temperature. This work focuses on modelling the microstructure and mechanical behaviour (especially fatigue) for additive manufactured NiTi actuators. Crystal plasticity finite element modelling based on electron backscatter diffraction has been implemented with a microstructure-sensitive fatigue indicator parameters to predict crack initiation. The framework presented provides a basis for predicting the effect of microstructure on the fatigue life of NiTi and will be further implemented to optimize the fatigue response under extreme conditions, specifically for multiaxial loading conditions of aerospace actuators.
Jozef McGowan | СŷÊÓÆµ of Sheffield
Analysis of Tool Wear in Tungsten Carbide During Titanium Milling Across Different Processing Routes
Co-authors: Alex Graves (Sandvik-Coromant), Jack Krohn (СŷÊÓÆµ of Sheffield), Martin Jackson (СŷÊÓÆµ of Sheffield)
Titanium alloys are vital in aerospace due to their strength-to-weight ratio and oxidation resistance, but are challenging to machine. WC-Co tools wear rapidly during titanium turning, primarily due to cobalt and carbon diffusion. However, wear mechanisms in milling are less understood. This study investigates early-stage tool wear during shoulder milling of Ti-6Al-4V using inserts with varying cobalt content. After ~8 minutes of milling, inserts were sectioned and analysed via SEM. Adhered titanium was observed on flank faces, and potential subsurface porosity was examined, offering insight into early wear mechanisms and their impact on tool degradation during milling.
1530 Poster Flash Presentations
7 | Akram Zarchini | СŷÊÓÆµ College Dublin
Real-Time Defect Detection in Sustainable Additive Manufacturing with Edge Computing Machine Learning Models
Co-authors: Andrea Villano (СŷÊÓÆµ College Dublin)
This study presents a machine learning-based approach for real-time defect detection in sustainable additive manufacturing. Sensor data from 3D printers are analyzed by trained models to identify defects such as porosity as they occur, enabling immediate corrective actions. The system reduces material waste, energy consumption, and production errors by detecting issues early in the process. Continuous model adaptation improves detection accuracy and minimizes false positives. This approach supports higher product quality, resource efficiency, and sustainable manufacturing practices.
8 | Usman Aziz | ATU Sligo
Mechanical, Microstructural, and Corrosion Analysis of DED-Repaired 316SS After Fracture
In this study, the repair performance of Directed Energy Deposition (DED) on fractured 316 stainless steel (316SS) samples is evaluated. Samples were first manufactured in flat, horizontal, and vertical build orientations and fractured through tensile testing to determine their initial mechanical behaviour. Following breakage, the specimens were repaired using DED with matching 316SS material. Subsequent mechanical testing, including tensile strength measurements, was performed to assess the recovery of mechanical properties after repair. Additionally, detailed fractography, microstructural characterization, and corrosion studies were conducted to understand the quality and integrity of the repaired regions. This work aims to provide insights into the mechanical, structural, and corrosion performance of DED-repaired 316SS components and to develop a deeper understanding of how build orientation and post-fracture repair influence the overall material behaviour. The findings are expected to support future applications of additive repair techniques in critical industries where 316SS is commonly used.
9 | Xibo Qin | Dublin City СŷÊÓÆµ
Effect of metal additive manufacturing process parameters on oxide build up
Co-authors: Rakesh Nair (Dublin City СŷÊÓÆµ), Lorna Fitzsimons (Dublin City СŷÊÓÆµ), Dermot Brabazon (Dublin City СŷÊÓÆµ)
This study mimics the recycled nitinol powder. The samples were heated at three different temperatures at different intervals in three grades of argon concentrations. An Oxygen sensor is attached to the outlet to monitor the oxygen concentration. A measuring system was used for calibration models using pyrometry to determine emissivity. Microstructures were monitored using an in-line camera during heating. Characterization techniques included SEM-EDX, microhardness, nanohardness, XPS, and OES. Results have indicated the effects of temperature on reflectance; a correlation between the effect of the processing temperature on oxidization; and the process parameters on the material properties of the powder.
- Refreshments and Posters | 1530-1600
- Session 2B | 1600-1700 | Chaired by , &
1600 Researcher Presentations
Mostafa Salem | СŷÊÓÆµ of Sheffield
Simulating defect formation during the 3D printing of Nickel-based superalloys
Co-authors: Miguel Espadero (СŷÊÓÆµ of Sheffield), Hugh Banes (СŷÊÓÆµ of Sheffield), Prashant Jadhev (СŷÊÓÆµ of Sheffield), Hector Basoalto (СŷÊÓÆµ of Sheffield), Yu Lu (СŷÊÓÆµ of Birmingham)
This study investigates the microcracking mechanisms in nickel-based superalloys with a high γ′ (gamma prime) content. Using a multi-component Phase Field (PF) model, the formation of nanopores during the Laser Powder Bed Fusion (LPBF) process was simulated. A decoupled Phase Field - Crystal Plasticity (PF-CP) approach was subsequently applied to predict the development of micro-residual stresses. The results revealed a strong positive correlation between the degree of nanoporosity in CM247LC and macroporosity in the final fabricated components.
Ajai Sankar | СŷÊÓÆµ College Dublin
Microstructural Evolution and Performance of LPBF Ti-6Al-4V Shell/Core-Lattice structures upon Hot Isostatic Pressing (HIP)
Co-authors: Fan Wu (СŷÊÓÆµ of Manchester), Haole Qin (СŷÊÓÆµ of Manchester), Ramesh Raghavendra (South East Technological СŷÊÓÆµ), Ahmad Farhadi (Croom Precision Medical), Shane Keaveney (Croom Precision Medical), Wajira Mirihanage (СŷÊÓÆµ of Manchester), Denis Dowling (СŷÊÓÆµ College Dublin), Mert Celikin (СŷÊÓÆµ College Dublin)
Additive manufacturing, particularly Laser Powder Bed Fusion (LPBF), has emerged as a revolutionary technique for fabricating complex structures. This study explores the effect of shell-core structures containing varying levels of retained powder (5–90%) on the densification, porosity, and microstructural evolution of Ti-6Al-4V alloys fabricated via LPBF and subjected to Hot Isostatic Pressing (HIP). The impact of internal lattice configurations and powder content on porosity control, microstructure optimization, and mechanical properties, particularly fatigue resistance, is investigated. The research finds that the volume density of lattice structures, combined with retained powder, influences grain coarsening, resulting in optimized microstructures with reduced porosity. These findings contribute to understanding the trade-offs between material properties, print productivity, and post-processing efficiency, offering new insights for enhancing the performance and scalability of LPBF-based manufacturing of high-performance titanium alloys.Thomas Gillick | Dublin City СŷÊÓÆµ
Residual Stresses in Nickel Titanium Cantilever Beams Manufactured by Laser Powder Bed Fusion
Co-authors: Sampreet Rangaswamy, Medad C.C. Monu, Dermot Brabazon - Dublin City СŷÊÓÆµ
Residual stress is a detrimental effect that stems from the Laser Powder Bed Fusion (LPBF) additive manufacturing process. It develops due to the complex heating/cooling conditions that occur during the printing process, and causes cracking, delamination, distortion, and generally diminished mechanical strength in printed parts. The objective of this project is to evaluate residual stress in cantilever beams fabricated from Nickel Titanium (NiTi), that have been printed by LPBF using a variety of printing parameters. Residual stresses are evaluated by measuring beam deflections and inputting these values into the corresponding beam mechanics equations to determine a stress value, based on the beam deflection. This project aims to provide a simplified method of recording residual stress compared to other commonly used methods.
1700 Poster Flash Presentations
10 | Merve Nur Dogu | Dublin City СŷÊÓÆµ
Investigation of Recrystallization and Grain Growth Kinetics of IN718 Fabricated by Laser Powder Bed Fusion
This study examines the recrystallization and grain growth behavior of IN718 alloy fabricated by laser powder bed fusion (L-PBF) under three different heat treatment temperatures (1050 °C, 1150 °C, and 1250 °C) and holding times (15, 45, and 90 minutes). Electron backscatter diffraction (EBSD) was used to characterize texture evolution. The as-built microstructure featured bowl-shaped melt pools, a chessboard-like grain pattern, and a strong cube texture {100}<001>. Recrystallization initiated at regions of high dislocation density—particularly melt pool overlaps and grain boundaries. At 1150 °C for 15 minutes, initial recrystallization was observed, with a texture transition to {122}<212> attributed to twinning-assisted mechanisms. Further annealing led to the expansion of recrystallized grains with minimal new twinning activity. Nearly full recrystallization occurred at 1250 °C, producing a weaker cube texture and a stronger P-orientation {011}<112>. Grain growth remained limited due to the pinning effect of non-coherent precipitates.
11 | Avinash Vitthal Borgaonkar | Dublin City СŷÊÓÆµ
Volumetric Energy Density Optimization and Phase Control in NiTi for Enhanced Sustainability and Functional Performance in Additive Manufacturing
Co-authors: David Kinahan (Dublin City СŷÊÓÆµ), Dermot Brabazon (Dublin City СŷÊÓÆµ)
This study explores Laser Powder Bed Fusion (LPBF) processing of NiTi shape memory alloys using a two-level design of experiments varying scan speed, layer thickness, and hatch spacing. The influence of volumetric energy density (VED) on part density, microhardness, surface quality, and phase formation were investigated. Higher VEDs (46.3–92.6 J/mm³) yielded near-theoretical densities (~98.9%) and enhanced microhardness (up to 297.67 HV), attributed to improved melting and reduced porosity. Excessive VED, however, led to localized grain coarsening. Surface roughness decreased at higher VEDs, and XRD/EDX analyses confirmed phase composition. These findings underline the importance of energy input optimization in LPBF-fabricated NiTi alloys.
Day two: Wednesday, 9th July 2025
- Session 3A | 0900-1045 | Chaired by , &
0915 Keynote talk
Dr Teresa Pérez-Prado | IMDEA
Additive Manufacturing of Energy Efficient Electric Motors
Assuming an average loss level of 5%, the amount of lost energy in the 8 billion electric motors in the EU alone is approximately 30% of the total energy consumption in Spain. Additive manufacturing (AM) of Fe-based metallic glasses could offer an alternative for producing e-motor components that help reduce these losses due to their excellent soft magnetic properties and near-net-shape manufacturing potential. However, significant challenges remain in processing these materials via AM, including controlling crystallisation to retain their amorphous nature, minimising porosity and residual stresses, ensuring good feedstock processability, and optimising magnetic properties through post-processing. Addressing these hurdles requires a multidisciplinary
approach combining materials design, process optimisation, and advanced characterisation.This lecture will review recent research on process parameter optimisation for the additive manufacturing of Fe-based metallic glasses and it will showcase strategies to precisely control thermal conditions during printing, minimising defects and preserving the amorphous structure in complex geometry components. It will be shown how a combined approach including computational modelling and experimental validation efforts might yield tailored processing conditions that can enhance the manufacturability and performance of Fe-based metallic glass parts. A discussion on how these advancements bring AM a step closer to enabling high-efficiency electric motors with reduced energy losses will follow.
0945 Researcher Presentations
Matt Williamson | СŷÊÓÆµ of Manchester
The Influence of Creep on the Initiation of Environmentally Assisted Cracking
Co-authors: Timothy L. Burnett (СŷÊÓÆµ of Manchester), Philip B. Prangnell (СŷÊÓÆµ of Manchester), Matthew E. Curd (СŷÊÓÆµ of Manchester), Juhi Srivastava (СŷÊÓÆµ of Manchester), Zak Barrett (Airbus), Nick Byers (Airbus)
7xxx series aluminium alloys are used across a wide range of transport applications due to their high strength and low density; however, these alloys are susceptible to Hydrogen embrittlement-related Environmentally Induced Cracking (H-EIC) when exposed to warm humid air. Studies into EIC have mostly focused on the propagation of cracks. However, studies on a variety of metallic alloys have highlighted the impact of prior low temperature creep exhaustion on the crack initiation process. This presentation will explore our current understanding of the effect of creep on EIC, and on-going work investigating this relationship in 7xxx series aluminium alloys.
Ramzy Abou-Zaid | СŷÊÓÆµ of Manchester
X-ray Computer Tomography and Microstructural Characterisation of Additive Structures for Advanced Repair of Aeroengine Components
Nickel superalloys are used in the construction of aeroengine compressor blades for their high temperature mechanical performance, as well as their resistance to corrosion and oxidation. Maximising the service life of these components is essential to lower costs and reduce waste. Laser Blown Powder Directed Energy Deposition (LBP-DED) is an additive manufacturing method that is being explored for the repair of these components. Due to their extreme operating conditions, any repair process must minimally affect the microstructure of the components to preserve the desired mechanical properties, as well as ensure any repair structures exhibit commensurate properties to the existing substrate.
Kate Bowers | СŷÊÓÆµ of Sheffield
Understanding the effect of wheel speed and feedstock morphology on grain size of commercially pure CONFORM copper wire
Co-authors: Martin Jackson (СŷÊÓÆµ of Sheffield), William Pullfrey (СŷÊÓÆµ of Sheffield), Eric B Goodall (СŷÊÓÆµ of Sheffield), Susanne Holly (Wieland Group)
The CONFORMâ„¢ process is a severe plastic deformation (SPD) technique and offers a promising route to produce high quality copper products from recycled feedstocks. This research investigates the use of solid and particulate copper processed through CONFORM, with a focus on understanding how feedstock morphology and process parameters influence consolidation, microstructural development, and final product quality. The work also explores the application of finite element modelling to simulate strain and temperature conditions during processing. This presentation will discuss the viability of recycled copper in continuous extrusion and its potential for enabling more sustainable, low-energy manufacturing routes.
Tom Cole | СŷÊÓÆµ of Sheffield
An Investigation into the Local Structure of Ni-33.at%Cr via Neutron Diffraction Methods
Short-range order (SRO), defined by non-statistical relations between atomic neighbouring, is known to influence multiple intrinsic material properties. Historically identification of SRO has been limited to changes in these properties, but without sufficient understanding SRO effects on material mechanisms their separation from microstructural affects is only implied. Recently, advances in Total Scattering Techniques have presented the opportunity for far more in-depth characterisation of local structure relationships in alloys. The present work looks to assess the local structure of Ni-Cr alloy via neutron diffraction, such to further our understanding of the ordering in systems forming the basis of Ni-superalloys and MPEAs.
- Refreshments and Posters | 1110-1140
- Session 3B | 1140-1300 | Chaired by , Ciaran Miles &
1140 Researcher Presentations
Lucas Cook | СŷÊÓÆµ of Sheffield
Analysis of the Relationship Between Wheel Speed and Grain Size of Aluminium Wire Produced Via the ConformTM Process
Co-authors: William J Pullfrey (СŷÊÓÆµ of Sheffield), Eric B Goodall (СŷÊÓÆµ of Sheffield), Martin Jackson (СŷÊÓÆµ of Sheffield)
The CONFORM process is a viable avenue for the production of low cost titanium from secondary sources. With research into the use of swarf as a viable feedstock showing that the CONFORM process can accommodate this change and produce viable fully consolidated wire from swarf. The possibility of the use of secondary sources of super-alloy material for the production of tooling allows a major step change to the economics of the process. This research aims to investigate the use of secondary materials on both the tooling and feedstock and compare the production of three different feed choices.
Yvonne Onowunmi-Kayode | Dublin City СŷÊÓÆµ
Laser Texturing of Ti-6Al-4V for Enhanced Anti-Biofouling and Hydrophobicity
This research investigates laser texturing as a method to alter the surface properties of Ti-6Al-4V with a focus on the wetting behaviour and fouling properties. Using laser ablation, micro-scale textures were fabricated on the surface, resulting in changes in surface roughness and wettability. The treated surfaces exhibited a transition from hydrophilic to hydrophobic highlighting the role of surface topography and chemistry in surface engineering. Results show that laser-based techniques can provide a precise, non-contact, environmentally-friendly surface modification method for introducing desired properties which are applicable in industries such as the medical industry which requires surfaces with anti-wetting and anti-biofouling functionalities.
Andrea Villano | СŷÊÓÆµ College Dublin
Use of in-process monitoring to evaluate porosity generated during the LPBF printing of Ti-6Al-4V spinal cage devices
Co-authors: Fatemeh Golpayegani (СŷÊÓÆµ College Dublin), Denis P. Dowling (СŷÊÓÆµ College Dublin)
Porosity generation at edges is a major issue in additive manufacturing. This study investigates sawtooth geometry influence on keyhole porosity generation for L-PBF printed Ti-6Al-4V spinal cages. Such porosity is believed to be linked to localised overheating due to the alloy powder lower thermal conductivity compared to that of the bulk alloy. Differences in microstructure between cage edges and bulk alloy supported those findings. An attempt to corelate porosity with changes in photodiode data involved the implementation of an in-process monitoring system, unfortunately no direct corelation was found. By implementing different sawtooth geometries, a shift in pore position was observed when altering the sawtooth dimensions.
Richard Thompson | СŷÊÓÆµ of Sheffield
Implementing Physically Realistic Fractal Surfaces into Analytical Rail Wear Models
Co-authors: David Fletcher (СŷÊÓÆµ of Sheffield), Adam Wilby (British Steel), Naomi Corteen (British Steel)
Contact between rail and wheel surfaces is a vital part of understanding rail wear. Without the ability to accurately model the rough surfaces involved, it is impossible to accurately model the system as a whole. Previous iterations of rail-wheel contact model have used several different contact representations, occasionally making use of profilometry data obtained experimentally. Implementing fractal roughness, where the surfaces are modelled as fractals based on Weierstrass-Mandelbrot functions resulting in mathematically infinite surface definition, could be more accurate. Several methods of implementing this have been developed and compared to previous subsurface stress distribution outputs.
- Lunch | 1300-1400
There will be the opportunity at this time to view the Poster Exhibition
From 1325 There will be a series of career talks from alumni and industry representatives
- | Bekaert | 2015 Cohort
- | Sellafield | 2013 Cohort
- UK Civil Service | 2015 Cohort
- | Halcor Ltd | 2018 Cohort
- Session 4 | 1400-1530 | Chaired by Darragh O Neill, Joe Hopkinson & Jacob Whittle
1400 Keynote talk
Dr. Ir. Mehrshad Mehrpouya | СŷÊÓÆµ of Twente
Additive Manufacturing of Shape Memory Materials
Over the past two decades, additive manufacturing (AM) has rapidly evolved, enabling unique design freedom and customization. A particularly exciting frontier in this space is the integration of smart materials with AM technologies—paving the way for four-dimensional (4D) printing. Unlike traditional 3D-printed parts, 4D-printed components can change shape or properties over time in response to external stimuli, adding the dynamic element of time as a functional dimension. Among smart materials, shape memory materials (SMMs) have emerged as key enablers of 4D printing. These materials, e.g., shape memory alloys (SMAs) and shape memory polymers (SMPs), can undergo significant deformation and return to their original shape, making them ideal for applications requiring adaptability and responsiveness. However, the additive manufacturing of SMMs introduces unique challenges. In materials like NiTi SMAs, even slight changes in composition or processing conditions can drastically alter transformation temperatures and functional performance. This sensitivity is especially critical in metal AM processes, where melting and solidification can significantly impact microstructure and thermomechanical behavior, often requiring complex postprocessing. Attendees will learn about the functional behavior of SMMs through case studies drawn from recent research, with a focus on both SMAs and SMPs. The talk will highlight how processing parameters influence material performance and discuss the broader implications of these findings. This knowledge can open new avenues for the design and fabrication of intelligent, adaptive products across diverse industrial domains—from biomedical devices to aerospace systems.
1430 Researcher Presentations
Xavier Ojeda | СŷÊÓÆµ of Manchester
Strain rate and temperature effects in slip activity in Titanium IMI834
Co-authors: João Quinta da Fonseca (СŷÊÓÆµ of Manchester), Philipp Withers (СŷÊÓÆµ of Manchester), Kate Fox (Rolls-Royce plc), Nigel Martin (Rolls-Royce plc)
Cold dwell is a time-dependent degradation process that can lead to the reduction of fatigue life of aero-engines. Cold dwell fatigue occurs in titanium alloys under cyclic loadings with dwell periods at peak stress below the yield strength. There are no measurements at the microscale that can demonstrate how this mechanism operates in an actual microstructure. Here, digital image correlation was used to investigate the material response to loading cycles at the micro-scale. Representative samples extracted from an actual forging were loaded to 80% and 90% of its yield strength, followed by a dwell period to induce creep at room temperature.
Meris Ikis | Dublin City СŷÊÓÆµ
Influence of chemical post-processing methods on the surface roughness of NiTi components manufactured by Laser Powder Bed Fusion
Laser Powder Bed Fusion (L-PBF) is increasingly used in additive manufacturing for its efficiency but often causes surface impurities like spattering and balling, leading to high surface roughness. This study produced NiTi cuboid samples manufactured by L-PBF and applied chemical polishing to reduce surface roughness. Etchant concentration and processing time were key variables, tested at three levels each. Design of Experiments (DOE) software was used to optimize these parameters. The aim is to evaluate post-processing techniques and optimize process parameters. Future work will refine L-PBF parameters to produce fatigue coupons and test the optimized chemical polishing conditions on them.
Ozgun Umut Tukac | СŷÊÓÆµ College Dublin
Using Uncoated Cemented Carbide Tools for Milling Ti64 Manufactured Using Differing Processing Routes
Co-authors: David Browne (СŷÊÓÆµ College Dublin), Mert Celikin (СŷÊÓÆµ College Dublin)
This study presents a novel alloy development approach to address challenges in the additive manufacturing (AM) of Ti-6Al-4V, widely used in biomedical implants. Conventional AM leads to columnar grain growth and strong textures, causing anisotropic mechanical properties. By implementing tailored alloying and optimized mixing techniques, this work aims to refine grains and achieve isotropic properties. Alloys were produced using inert gas arc melting (IGAM), with preliminary results showing improved microstructure uniformity and texture control. These outcomes suggest a promising pathway for producing Ti-6Al-4V components with enhanced structural and mechanical performance for biomedical applications.
1530 Prize awards and closing remarks
- Experience VR Session | 1600-1700
Part of a project run by Dermot Brabazon, please sign up at registration
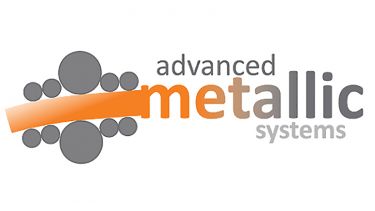
Study with us
Study for a fully-funded PhD or EngD in Advanced Metallic Systems to explore innovative materials and manufacturing routes to increase sustainability and performance.